Coastal residents across the nation face strict zoning regulations when it comes to building a dream home, especially in high-density areas where land is at a premium.
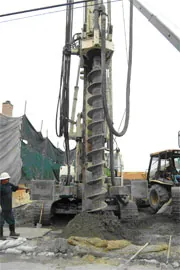 |
When constructing a secant pile wall using the CFA method, an auger rotates through the sand and soil causing no vibration, making it safe for surrounding foundations. |
In Southern California, a 5,000-square-foot beachfront lot equates to a 2,500-square-foot footprint and in many coastal areas there are restrictions as to how high you can build. The only way to gain square feet of living space, when you cannot build up, is to use a system that makes it possible to build down.
The inherent risks associated with normal foundation construction quadruple when constructing a living space below ground. Most builders would agree and often tell their clients that building a lower-level living space is not an option. The reason is, with just one mistake, the potential damage to adjacent foundations and underground utilities from ground displacement or undermining could cost millions.
There are only two shoring methods available to builders wanting to build a basement in a high water table. However, there is only one method that is safe in high water and high-density areas.
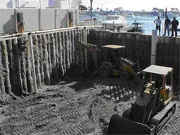 |
The CFA system of building coastal basements creates a safe and dry work environment for constructing a 100% waterproof lower-level living space. |
The first technique uses interlocking sheet piles that are driven or vibrated into the ground. The pitfalls to this method are the constant vibration created that can cause damage to nearby foundations. It can also rattle the structure causing damage to personal property inside and out of the dwelling. The vibrations can also trigger a process known as ground liquefaction where the soil becomes liquid or loose.
The second technique uses a secant pile wall. Although a conventional piling rig can construct a secant (overlapping) piled retaining wall, the method of installation is problematic in a high-density area too. The main issue with this installation process is the risk of undermining. The conventional method of installing a secant pile wall is to remove all the sand and soil to create a shaft. An open shaft has the potential to collapse. If the area does collapse, any nearby structures are in danger as their foundations can crack or slip.
Now there is a new method of installing a secant pile wall that is more cost effective and can safely be used in high-density coastal areas. This process is only new in the United States; it has been used in Europe for 25 years. The Continuous Flight Auger (CFA) system has been in use since 2001 in California for secant piles.
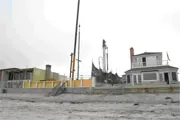 |
This meticulous method of building basements provides valuable living space that will increase the style and function of your home. |
The secant pile system, using CFA techniques, has proven very effective at overcoming the problems experienced by other methods. Contractors in the United Kingdom have increasingly used CFA techniques to further improve productivity of this type of piled wall. The improved capabilities of piling rigs, as well as developments in concrete technology and instrumentation, have made secant piled walls possible.
When constructing a secant pile wall using the CFA method, an auger gently rotates through sand and soil to the desired depth. During the auger's transit no vibration is produced. This is important, as we discussed earlier. Once the auger reaches the target depth, a special concrete mix is pumped with constant pressure through the hollow stem of the auger. Constant pressure is paramount during the auger's extraction. The high-pressure prevents any void from occurring in the ground as concrete is placed, creating a new CFA pile.
Maintaining pressure is so important that the use of sophisticated instrumentation is required while constructing CFA piles. The system also aids the operator in constructing the pile during both the auguring and concreting phase. The system maintains a detailed record of the construction process that can be shared with construction inspectors and engineers.
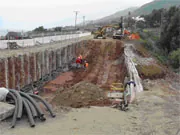 |
The Scheffler system of creating coastal basements involves constructing secant pile walls, then excavating and dredging out the sand and soil, leaving the natural ground water in place. Next, a heavy concrete slab is placed below the water, keeping any natural ground water from entering the system, and the trapped water is removed. |
With the latest development, it is possible for the computer to control the rig directly and construct the pile to a preset parameter. However the operator can over-ride the auto control at any time if there is a problem during installation. With a properly instrumented CFA pile, there is never a void or any subsidence around the pile. This is why it is the single most important part of our CFA pile system and makes it safe and successful.
Once the secant piles have cured, the sand and soil will be excavated and dredged out, leaving the natural ground water in place. Then a thick, heavy, concrete slab is placed below the water keeping any natural ground water from entering the system. The trapped water, within the enclosed structure, is then removed and the shoring process is complete. With a safe and dry work environment the builder can begin constructing a 100% waterproof basement.
There is no better way to add valuable living space in coastal communities. The Scheffler system is quick, competitive and uncompromising. There is no other system that mitigates the risks as well as Scheffler's system.
Dale Scheffler is the founder of D.J. Scheffler, Inc., a corporation that specializes in deep foundation drilling and earth shoring systems. D.J. Scheffler, Inc. has provided quality foundation drilling and earth shoring systems for 25 years and was the piling contractor chosen to perform the work for the new Skywalk Bridge in the Grand Canyon.
Here are some related articles:
View Other Related House Plans:
Save this article to:
back to top